4 reasons for carbon refinement with real carbon
Whether Full carbon or finishing with real carbon is, in a way, a question of faith. True weight fanatics swear by parts made of full carbon, i.e. a component that consists entirely of carbon fiber fabrics and webs as well as resin. But why is full carbon not always sensible? We give you 4 reasons for carbon refinement with real carbon and against Full carbon.
1) Carbon thickening looks like full carbon
Carbon finishing odhe also Carbon coating is a procedure in which a existing component a Schicht off Real carbon aufgetragen is used. This is not a cheap film or water transfer printing, but exactly the same material that is used for full carbon parts. Just like a full carbon part, the real carbon is processed with a resin and sealed with the same clear coat. This of course also creates exactly the same optics at lower costwhich are the main reason for carbon finishing. When installed, even a professional can hardly distinguish between carbon finishing with real carbon and full carbon. How could they, since the top layer is the same material?
Can you tell us if the components shown have been finished with real carbon or are full carbon?
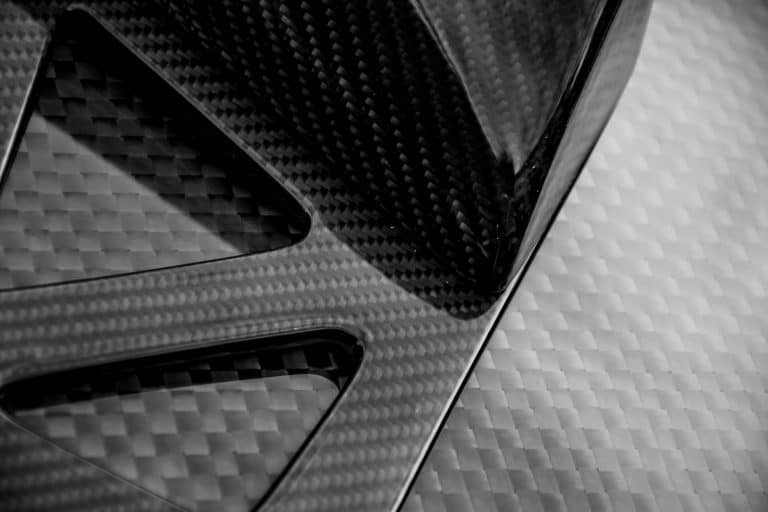
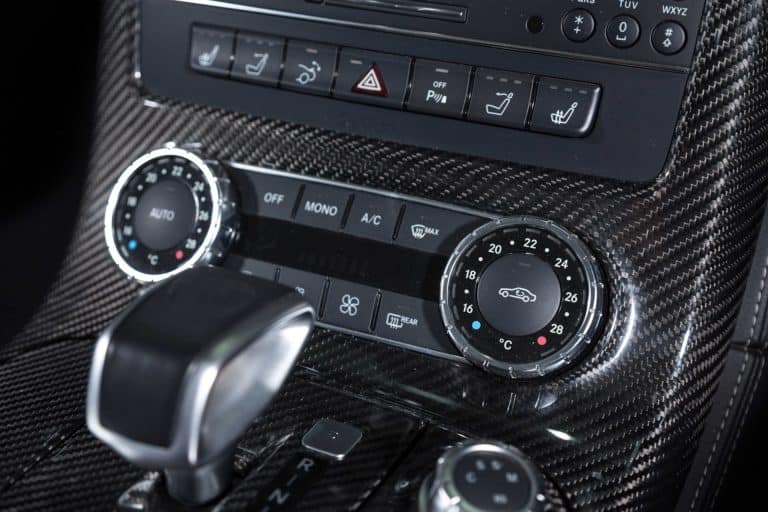
2) Carbon finishing costs much less
Full carbon parts always require a Negative form. This mold must be molded from an original component, which means that if you want to have full carbon mirror caps made for your vehicle, the service provider must mold your existing mirror cap. Creating a mold is a very labor- and material-intensive process, as the quality of the mold determines that of the subsequent full carbon part. Molding also always poses a risk to the original part, because if the release agents used do not 100% do their job - which is to simply release after the mold is created, can damage to the paintwork can occur, destroying the master model or rendering it unusable. These risks do not exist with carbon finishing.
The function must not be forgotten
It must also be remembered that the components have both an outer and an inner shape. Interior trim or mirror caps usually have small retaining lugs and clips, which should also be present on the full carbon part. The function of the component must be exactly the same as the original, because what is the point of a full carbon part that cannot be attached? The only sensible solution here is usually to glue a full carbon part onto the old part, as is done by OEMs in large numbers. However, this depends on the type of fastening and the output quantity.
3) Does weight really matter?
In 90% of cases, no! Interior trim, fascias, spoilers and the mirror caps just mentioned are mostly made of plastic. ABS plastic, for example, has a minimally lower density than full carbon. This means that the weight saving is not only zero, but even negative. The carbon part ends up weighing more than the plastic part! Even with carbon finishing, the part weighs a little more afterwards because a layer of carbon is applied. The 10% of worthwhile cases relate mainly to steel or aluminum sheet metal components such as fenders, tailgates or the vehicle roof. Here, due to the higher density of steel (5 times denser) or aluminum (about 1.7 times denser), quite a bit of weight can be saved. Particularly in the roof area, the lower density of steel and aluminum makes it much more efficient. Center of gravity height and the resulting better handling, it makes perfect sense to install a carbon part. But even here, the benefit relative to the cost is rather small and really worthwhile only for enthusiasts. We do not want to say at this point that full carbon is bad, quite the opposite. As we explained in our article on Thema "What is carbon?" explained, the mechanical properties of carbon are very impressive, but are not usually needed, so carbon finishing is a good and inexpensive alternative.
4) Carbon finishing with real carbon is faster
Full carbon parts always need a negative mold, as already mentioned. This also means that the workload increases simply due to the additional work steps. Planning should also not be underestimated, because not every component can be molded in one piece, so the parting lines need to be well planned in advance. Provided that no negative mold is available, however, carbon finishing can be carried out more quickly, as fewer work steps are required due to the process. Once the goods have been received, you can reinstall the freshly finished component in your vehicle after just 2-3 weeks. However, depending on the service provider and workload, this can be much faster. Alternatively, you can directly order a carbon finished part in exchange for the old part if it is in stock.
Conclusion
In most cases, full carbon is not the right way to go and exactly the same look can be achieved by carbon finishing with real carbon. This is reflected, among other things, in the fact that many OEMs use carbon finishing (applying a full carbon part to a substrate) for their carbon interiors. This also includes premium OEMs such as BMW, Audi, Mercedes and Volkswagen. Of course, when removed, it is obvious to everyone that a component has only been refined and is not made of full carbon. But how often will someone look behind the scenes and check whether the mirror cap is really made of full carbon, or even: Who cares? Because there is nothing objectionable about carbon refinement with real carbon. Furthermore, the mechanical properties of full carbon and the low weight are almost never needed. So why spend money on something you don't need? Instead, you could refine other parts on the vehicle with carbon. Let's summarize: You save money as well as time and end up with a component that is indistinguishable from full carbon when installed. In our eyes: the better choice in most cases!
Would you like to learn even more about carbon? Then read our article on the question: What is carbon fiber?